Diver Propulsion Vehicle
A Diver Propulsion Vehicle (DPV) is a device that tows a scuba diver at
speeds of up to 2.5 mph underwater or on the surface. It is a small, torpedo shaped,
cylinder approximately 8 inches in diameter and 36 inches long. The diver holds onto two
handles at the back which contain switches for the motor and underwater headlight. When in
use the diver's body streams out horizontally behind and above the DPV allowing the
propeller wash to flow under the divers body.
Propulsion is generated by a 1/3 HP permanent magnet DC motor running at 3600 RPM. The
electrical power comes from two 12 volt 14 amp hour batteries, wired in parallel, which
provide 12 volts at 28 amps. The motor shaft is stepped down through a custom 4 to 1
geared speed reducer to a shaft speed of 900 RPM which drives the two bladed propeller
directly. The battery system also includes a sealed chamber for palladium catalyzers to
hydrogenate the H2 and O2 given off by the batteries back into
water droplets. The propeller includes a Kort nozzle which is a shroud around the propeller
which improves its efficiency.
The pressure shell is made from a 0.156 inch wall thickness, 8 inch OD 5052-H32 aluminum
tube welded to a custom machined nose cone and tail section made from 6061-T6 aluminum.
The nose cone includes a housing for a 100,000 candlepower underwater light. I was
responsible for the entire project from the initial concept, through mechanical design,
stress analysis, fluid dynamics analysis, assembly and testing. I did have assistance from
other ME students, primarily for testing, but also for a small amount of the design. The DPV
pressure shell, fore and aft static O-ring seals, and propeller shaft dynamic seals were successfully tested in a pressure simulation
chamber at the Garfield Thomas Water Tunnel to a depth of 300 feet. It has also been used
successfully on numerous dives since then. As a prototype, this device was equivalent, in
features and capability, to the best devices that you could buy at the time. The
hydrostatic pressure test chamber was interesting in its own right, it was a
section cut out of a 16" battleship cannon and could be used to test devices
to a depth of 20,000'.
This project was undertaken as a junior and senior Mechanical Engineering design project at the
Pennsylvania State University. In addition to all of the theoretical courses, there was a
three course sequence where you had to actually design and build something. Normally they
had suggested projects which were less ambitious, but of a scope that would fit within a
single design course. If you had your own ideas they were willing to listen, and they
thought this was a great idea. I, on the other hand, had no idea what I was getting into.
This project would consume my life for the next two years, and I loved it! Designing
the DPV was the highest high I had ever experienced -
this is why I became an engineer!
Diver Propulsion Vehicle
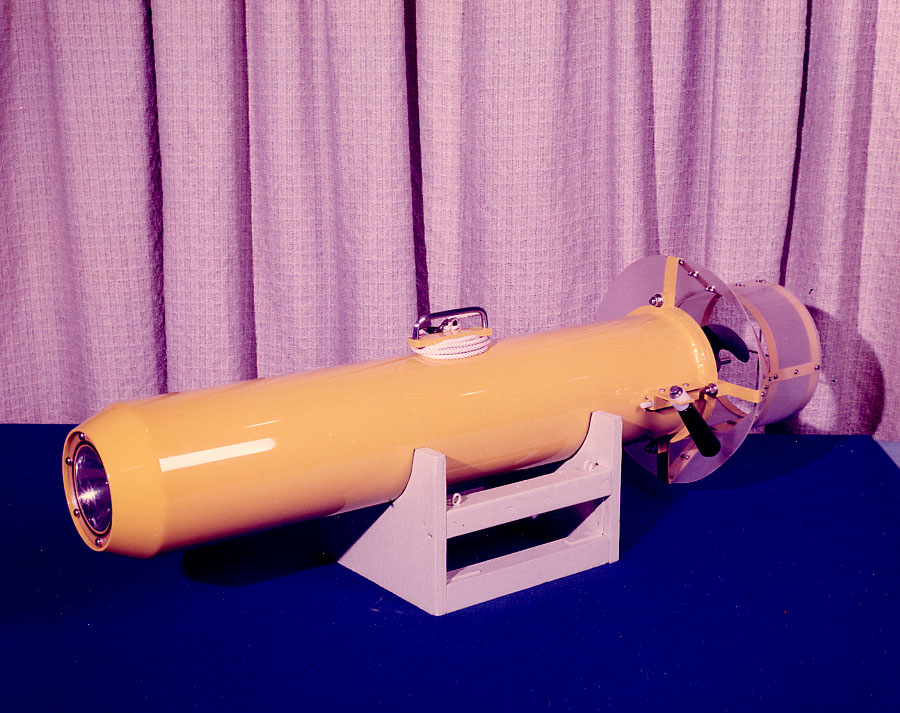
Batteries
and palladium catalyzers
Drive train including electric motor and 4:1 speed reducer,
aft pressure shell, seals, and propeller
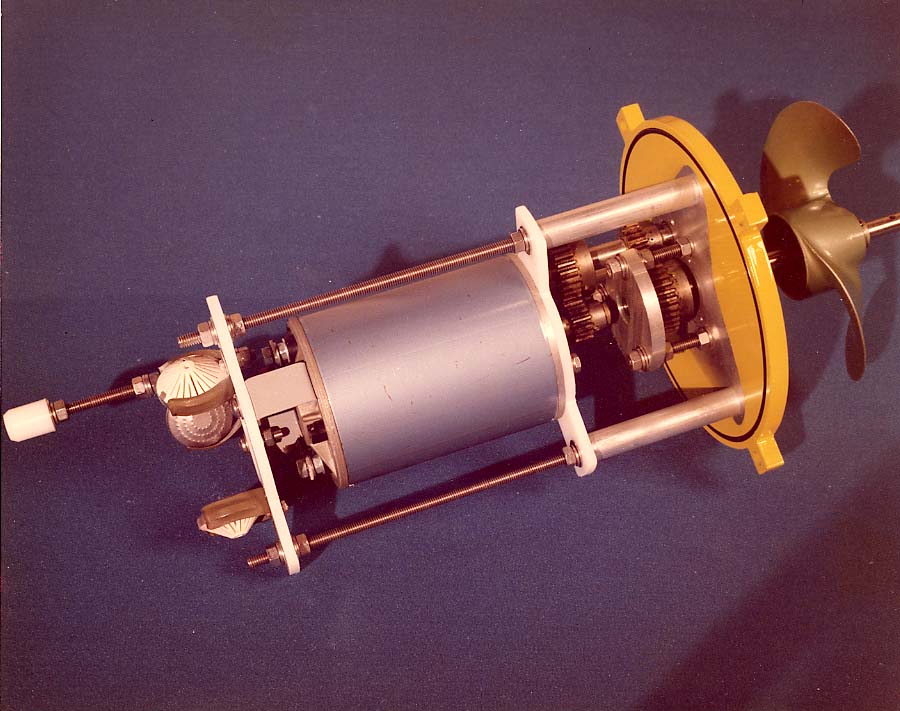
|